WoodSeer - Predicting Inner Wood Defects from Outer Bark Features

The WoodSeer project has been funded by the French ANR and coordinated by ThiƩry Constant from INRAE. Its purpose is to evaluate the use of machine learning to predict the interior distribution of defects inside roundwood from the external geometry of the wood.
Tree semantic features detection from X-Ray images
Work by Salim Khazem
Within the project, several pipelines are developed to detect and predict tree semantic features such as centerlines, contours and knots. The images below show the output of different pipelines used to detect the centers, contours and knots from X-Ray images. For the centers, the task was approached as a regression problem to detect the coordinates (x, y) of the centers. For the contours and knots, the task was approached as a segmentation problem.
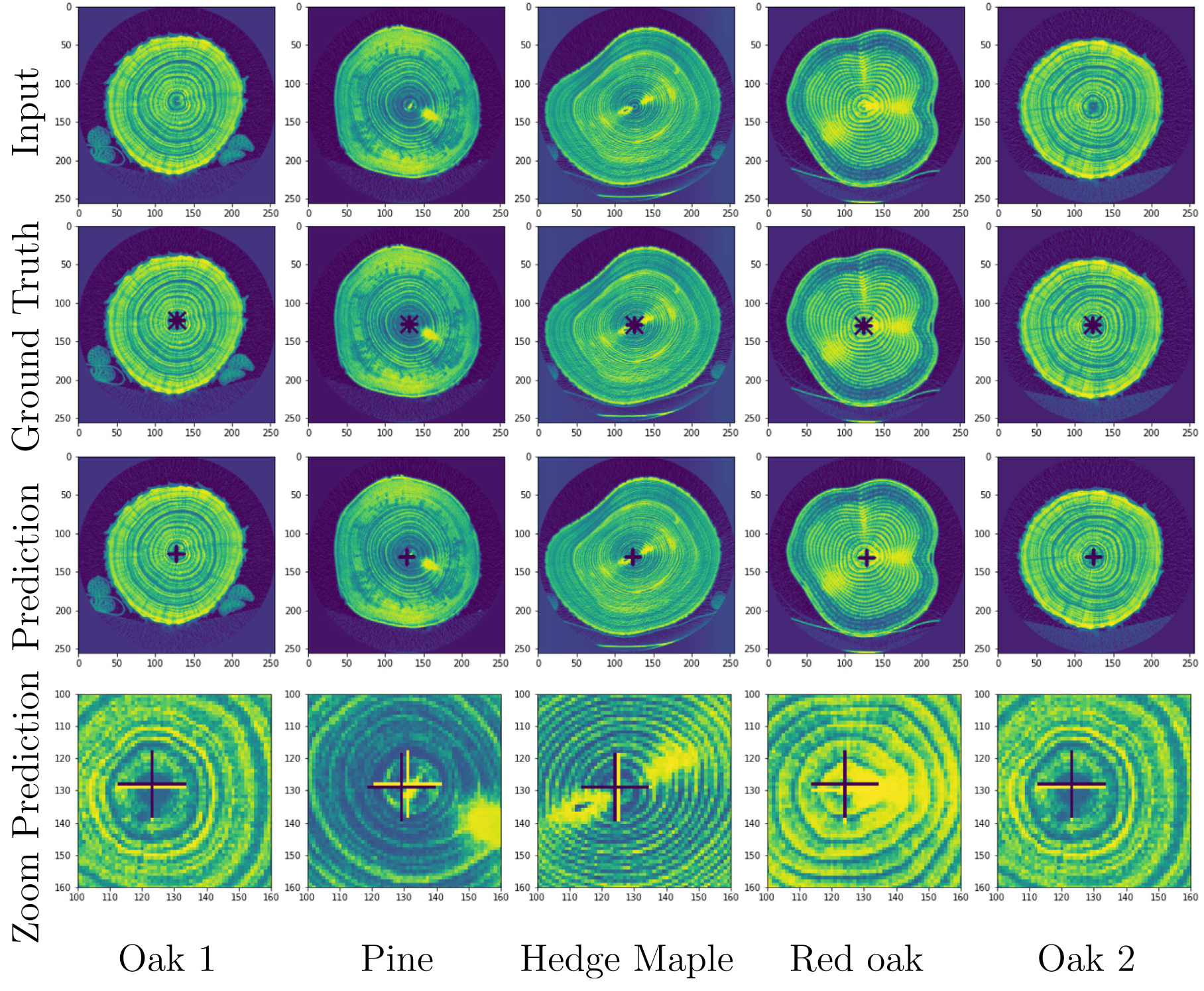
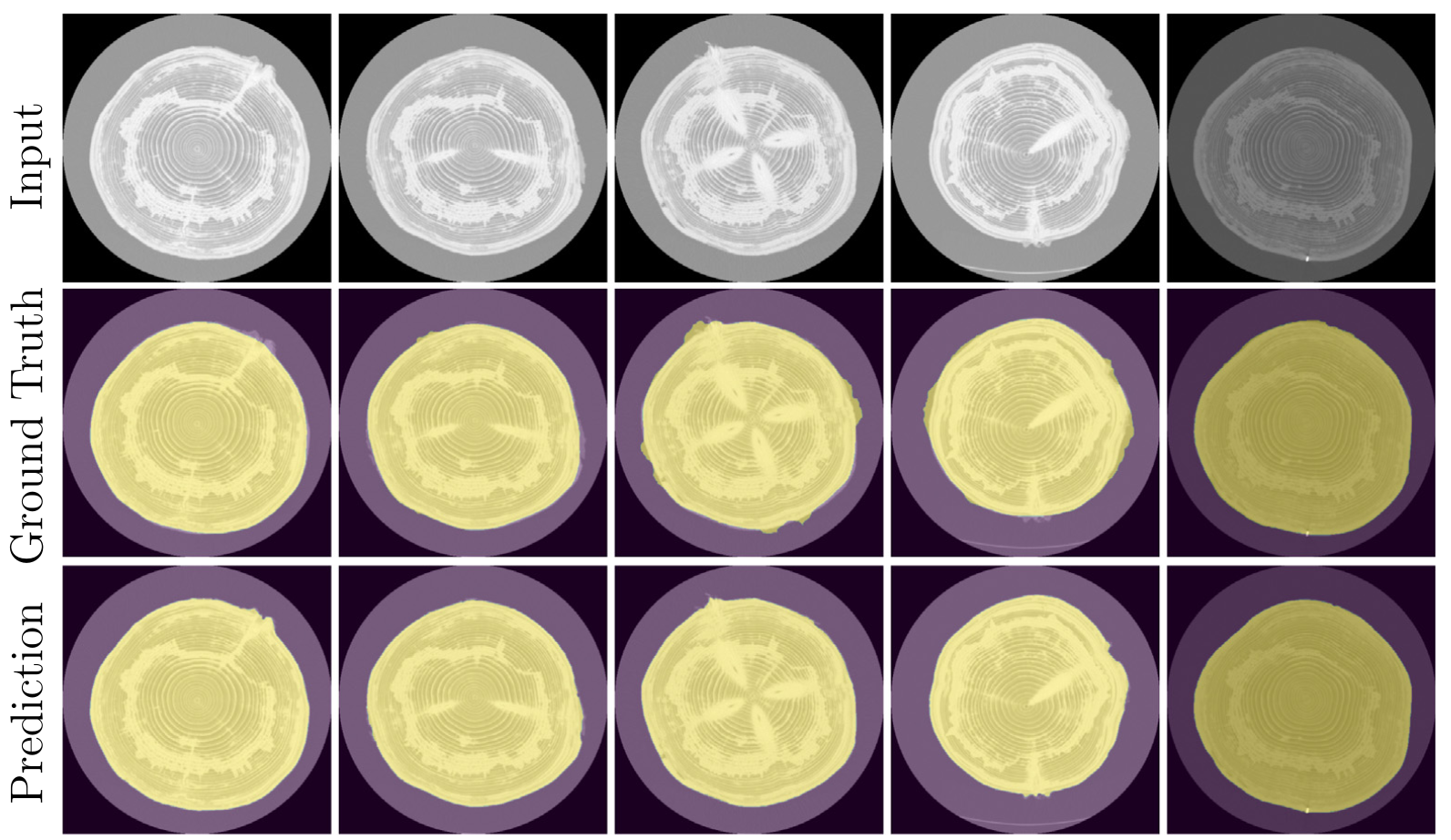
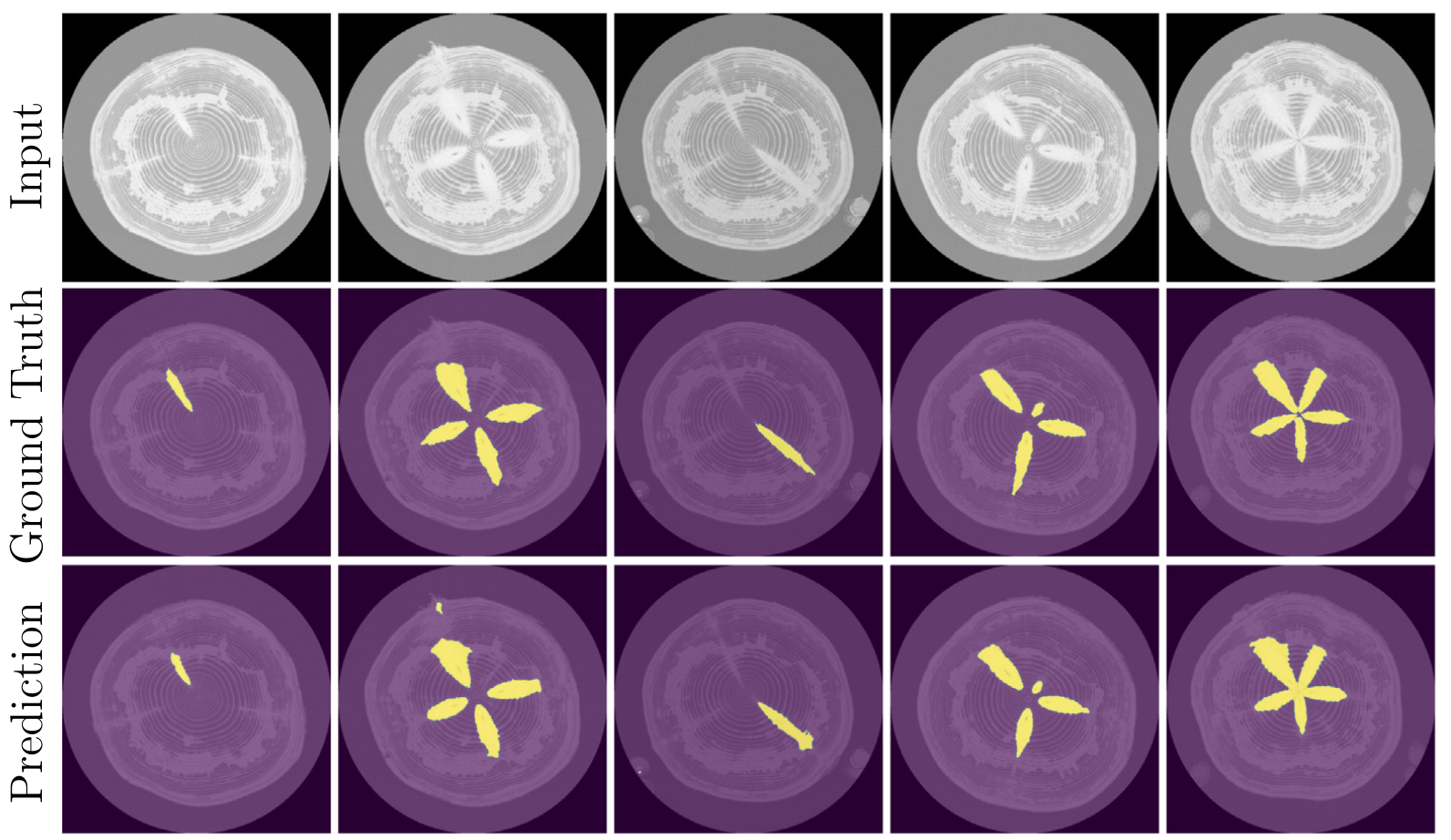
Knots prediction from the outer-surface of wood log
Work by Salim Khazem
The pipeline developed in this section aims to predict internal defects using the outer surface of wood logs. It takes a thin line of contours as input to predict the mask of knots. Experiments were conducted using two species (Spruce and Fir) and the results are shown in the figures below. The pipeline is an encoder-decoder, the encoder is composed of ConvLSTM blocks to take advantage of both spatial and reccurent features extractors.
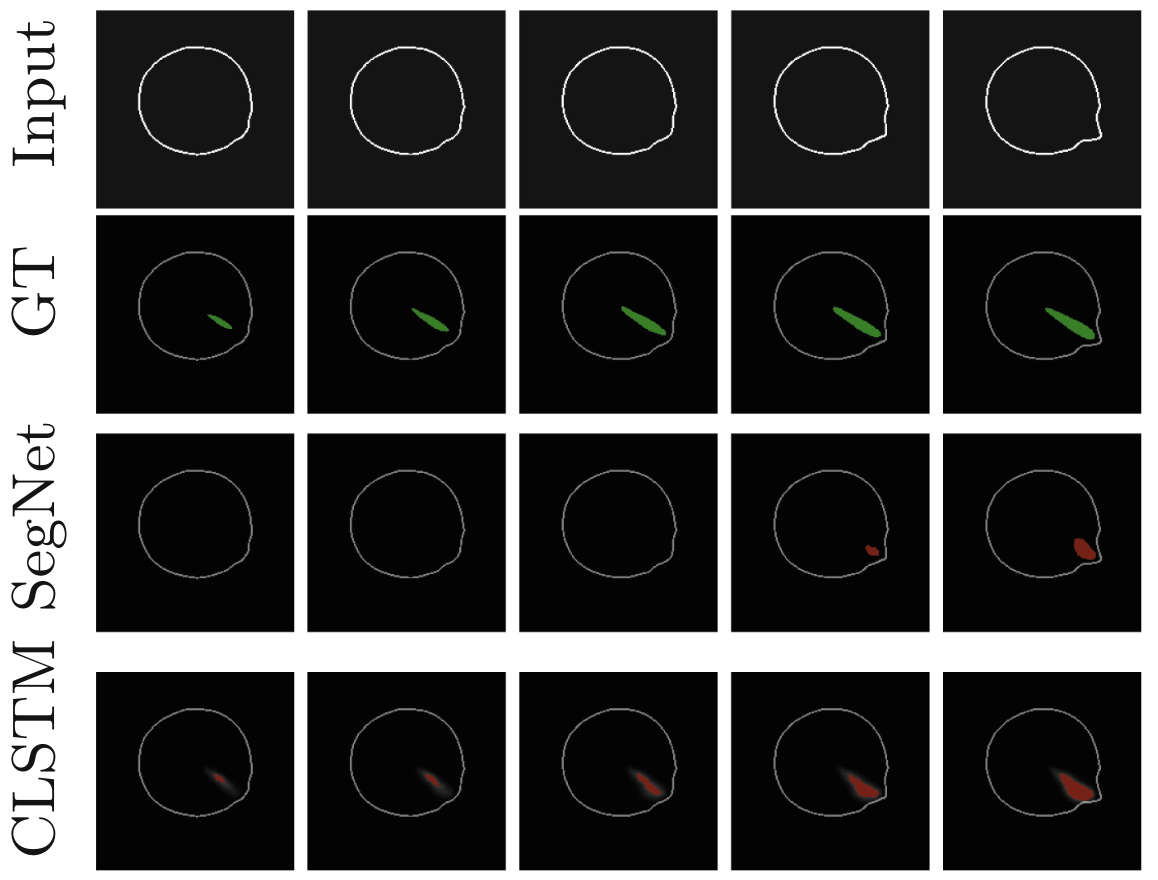
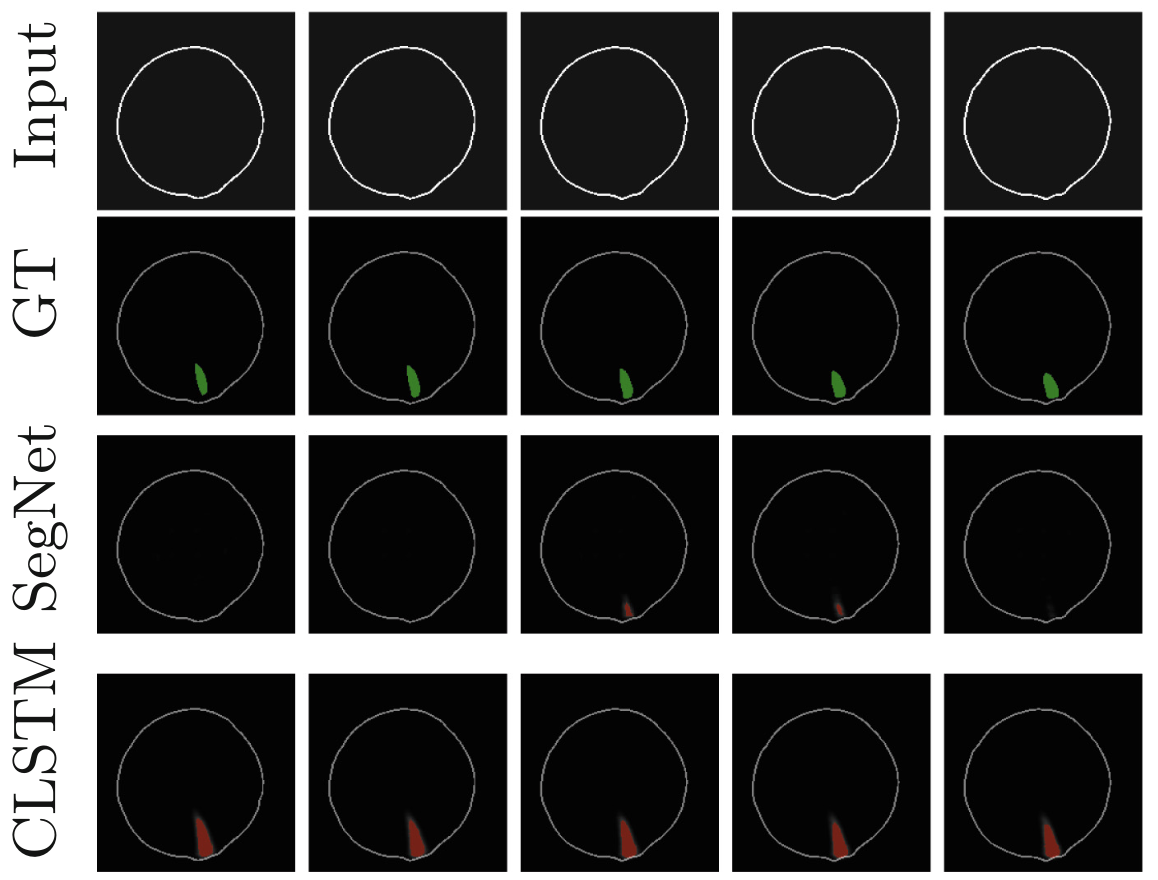
The results below show the 3D representation of the output, Paraview is used in this case. The Blue part indicates the prediction of the model, while the Red part represents the ground truth.
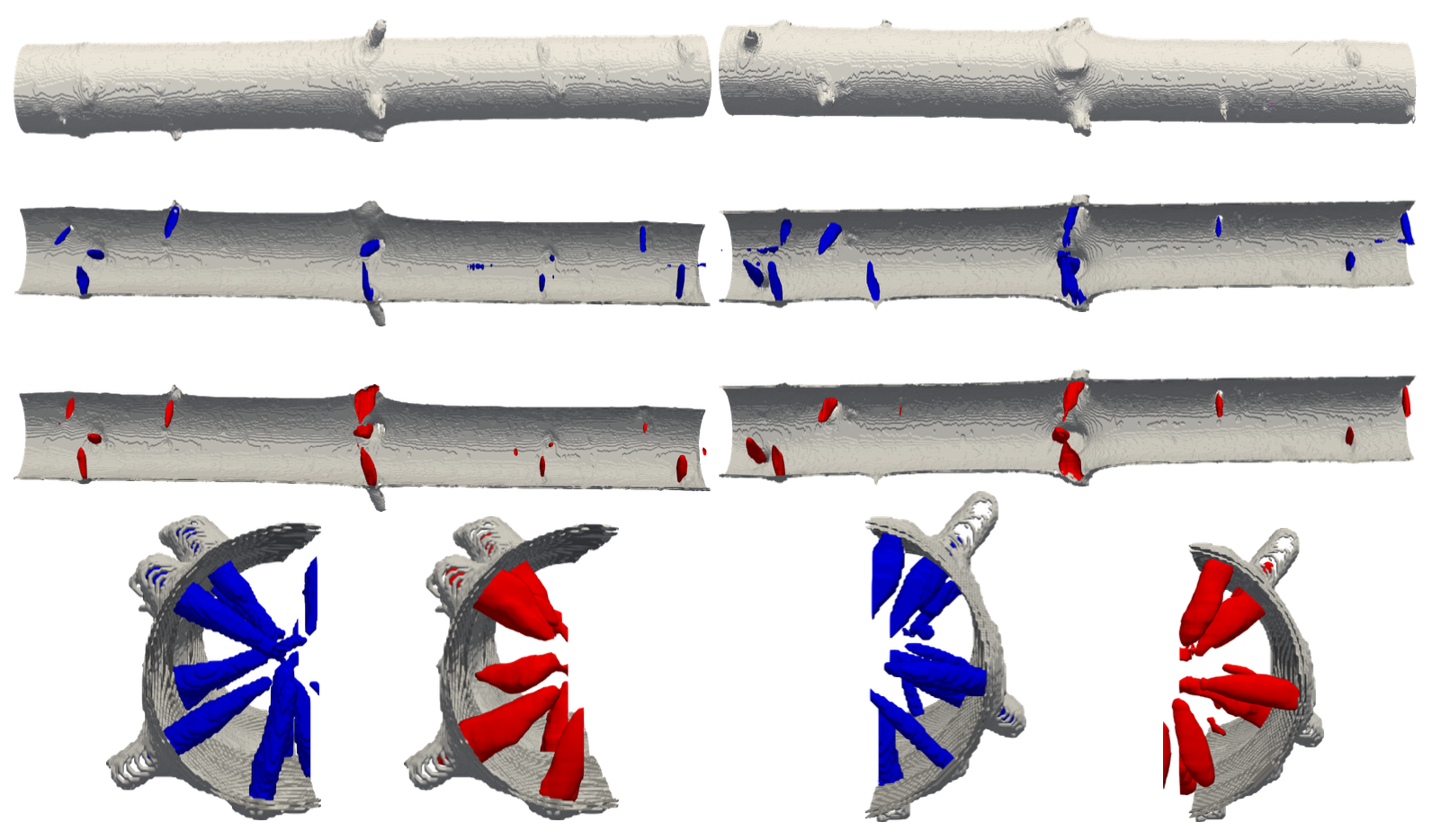
The videos below Show the 3D representation of the output, Paraview and CloudCompare are used in these two cases. The Blue part indicates the prediction of the model, while the Red part represents the ground truth.
The first video is the representation of Spruce Specie:
The second video is the representation of Fir Specie:
Design of a specialised tree scanner
The tree scanner concept can be illustrated in the video below, in our simulation environment. It consists of a rigid frame carrying 8 laser profilers and 4 cameras, moving around the tree.
Knowing the geometry of the sensor placement and the sensor properties, it is possible to build a 3D model and link the 3D coordinates of points with their image coordinates.
A significant challenge resides in the extrinsic calibration of all these sensors. Once they are well calibrated, the 3D model collected from the profiler should project precisely on the image frames. This is illustrated by the blue points in the figure below, projecting onto the calibration board used for this system.
Relating the 3D points to their camera coordinates allows creating a 3D point cloud of a given tree (lighter tree in the video below). From this pointcloud, producing a 3D mesh is achieved with VoxBlox. The geometric mesh appears in green, but VoxBlox can also produce a colored mesh seens as a darker tree in the video.
This final video shows three trees captured with our method. Small floating objects around the first tree results from the sun interacting with the profilers and creating artefacts. Proper shading made these artefacts disappear for the other trees.
3D reconstruction from video streams
Work by Aishwarya Venkataramanan.
Within the project, several techniques for tree geometry reconstruction will be evaluated, from portable laser scanners to computer vision. The image below shows the reconstruction achieved using image sequences captured with a DJI Osmo pocket, processed with ColMap after our own pre-processing. A zoom on the reconstructed surface and its wireframe is also visible.
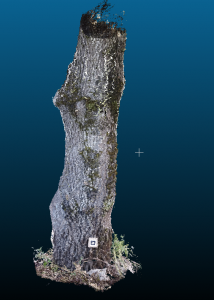
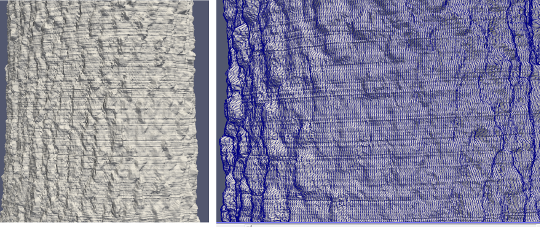
The reconstruction precision has been evaluated in comparison with 3D point couds acquired with a laser scanner:
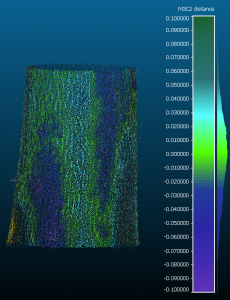
Bark texture reconstruction and generation
From the generated bark, it is possible to extract a texture map, which corresponds to the unrolling of the bark:
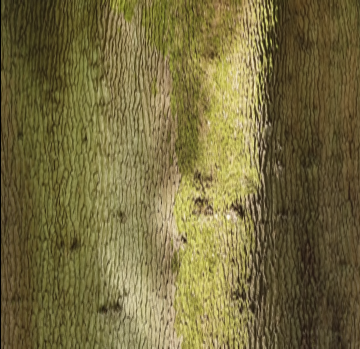
From this texture, it is possible to train a GAN to generate artificial textures:
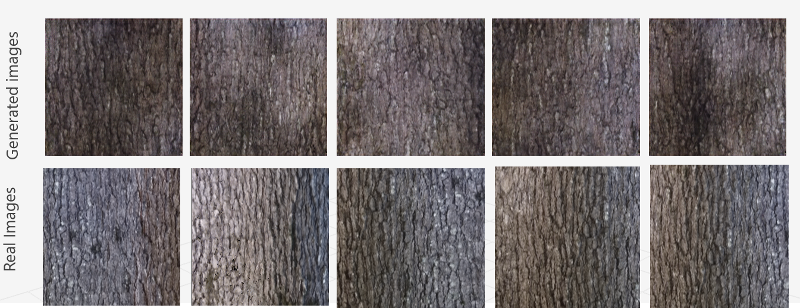
Interior structure prediction
Work by Mohamed Mejri
Predicting the interior density of the wood from the exterior geometry is one of the long-term objectives of the project. The image below show the output of a 3D network (UNet3D in this case but we tested others) from the wood surface geometry for toy examples. The images shows the iso-surface of density corresponding to simulated density, generated with ParaView. The blue surface is the ground truth whereas the red surface is built from the density predicted by the network.
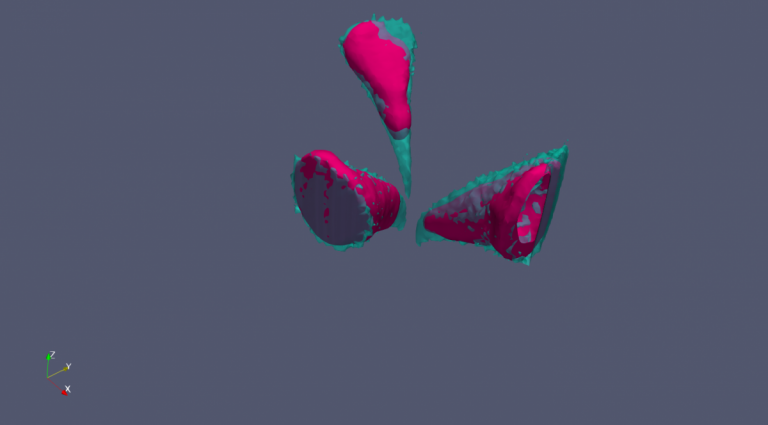
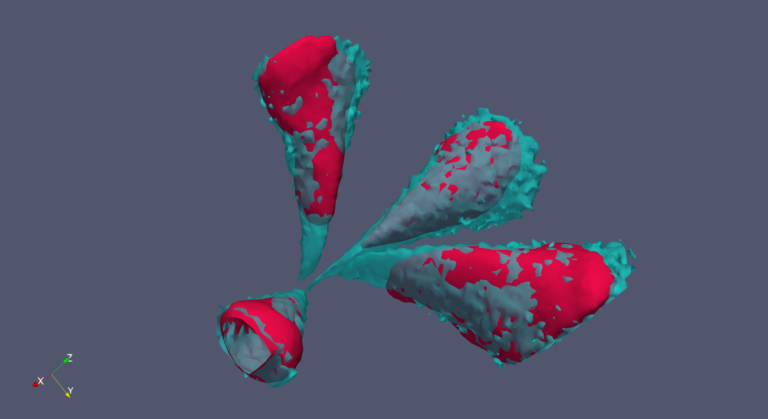